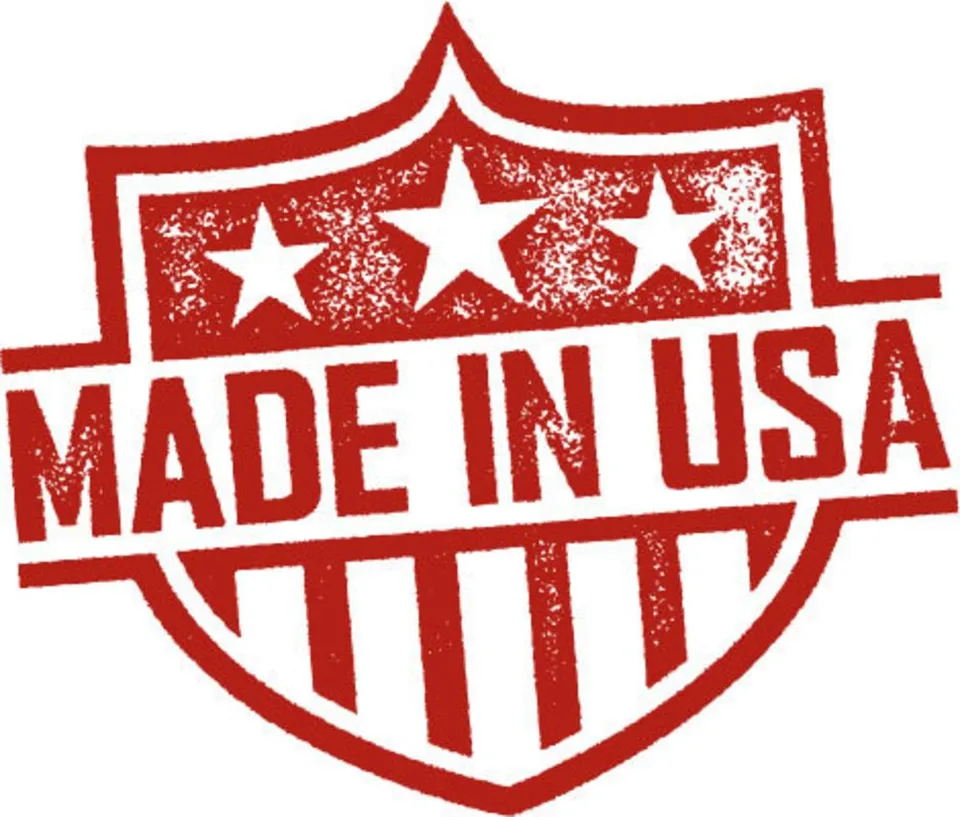
Made in USA Vintage Shield. (Photo Credit: Apparel Business Systems)
How It Took a Global Pandemic & a War to Make it Happen
For years U.S. politicians have been promising to bring manufacturing back home, in an attempt to help strengthen our economy and bring jobs back to our shore; but they were always empty promises.
In the 1960s, the U.S. was responsible for 50% of the world’s manufacturing output (hard to believe, right?), but today the number is a pitiful 17% . In 1979, there were approximately 20 million manufacturing jobs in the U. S. and today, sadly, there are less than 12 million. So, what went wrong? Why did we lose our manufacturing capabilities across the board?
The manufacturing industry once generated a number of steady, higher paying jobs, creating a healthy middle class, as well as labor unions. It also widened the gap between rich and poor. Many immigrants came to the U.S. because there were so many jobs available. Where once industrialized cities such as New York City, Buffalo, Cincinnati, and Cleveland were among the top ten in population, today, they are only shadows of their former manufacturing selves.
“The inner cities and the rural towns were really basically decimated,” said Sandy Montalbano, a consultant with the Reshoring Initiative, an organization that was formed in 2010 to help bring back manufacturing jobs to the United States. In an interview with 60 Days USA she claimed, “These were really good-paying jobs with benefits and these wage earners were able to provide for their families.”
The United States dominated the manufacturing market worldwide until the 1970s. So, if the U.S. was such an industrial powerhouse, why did American manufacturing go offshore? What happened?
Sadly, there were a number of factors that contributed to the decline in manufacturing in the United States.
Beginning in the mid-Eighties, and throughout the early 2000s, many manufacturing jobs went “offshore” as companies took advantage of lower wages and fewer regulations.
According to Montalbano, these companies were focusing on short-term gains for shareholders instead of investing in capital equipment, innovation, and workforce training. Another factor was the federal government, it allowed the U.S. dollar to appreciate 300 percent vs. our trading partners over the past 40 years, which caused the U.S. dollar to become overvalued.
These factors were all compounded, Montalbano adds, when the country began to promote a “college for all” education system, putting less emphasis on ‘skills-based’ training, credentialing, and apprenticeship. UoF has been actively trying to help re-educate people with their digital and on-the-table video library of 500+ lessons.
Consumers also had a hand in manufacturing jobs going offshore, by demanding and buying the cheapest products available. This caused a trade deficit, which means the amount by which the cost of a country’s imports exceeds the value of its exports, which continues to impact the manufacturing industry in the U.S.
Obviously, bringing manufacturing back to life in the United States will stimulate the economy and create plenty of job opportunities. In recent years, some promising numbers indicate that certain industries are willing to bring manufacturing back to the U.S., a hopeful and encouraging sign, but it will take more time, money and lots of effort.
According to a 2020 Reshoring Initiative report, approximately 1 million manufacturing jobs returned to the United States from 2010-2020.

Made in the USA image. (Photo Credit: Getty Images)
These are all promising signs, but while manufacturing nationwide increased 20 percent from 2009 to 2017, employment in the fashion industry only increased by 5 percent. Montalbano says there are a number of things that need to be done to rev up the nation’s manufacturing sector. “The government needs to level the playing field,” Montalbano said. This can also be achieved by fine tuning the American manufacturing industry with automation and other new technologies, as well as investing in properly training the workforce through processes such as apprenticeships and vocational education. According to Montalbano, “Workers are going to need more than a high school education. There needs to be lifelong learning because technology is moving so quickly.”
The Reshoring Initiative sees an encouraging trend as U.S. companies are gradually turning away from offshoring and returning to U.S. manufacturing. American companies are beginning to weigh the pros and cons of manufacturing offshore: quality control issues, increased transportation costs, fair trade and labor issues in other countries and concern over a company’s carbon footprint and public image when it comes to sustainability.
In an article published in Industry Week, Harry Moser, the founder and president of the Reshoring Initiative, said the push to bring back jobs initially got off to a good start under Trump, due to tax cuts and reductions in regulations, however, his tariff policies and other uncertainties put a damper on that progress.
Ironically, the COVID-19 pandemic actually helped U.S. manufacturing. Moser stated that the pandemic encouraged local production with shorter supply chains and fewer people handling merchandise.
Moser is more optimistic about the administration of President Biden, as Biden has promised 5 million new manufacturing jobs. Moser said the nation will need to reduce manufacturing costs, improve worker skills, and strengthen the U.S. dollar to get there.
One of the easiest manufacturing categories to bring back “onshore” would be fashion. While the fashion industry in the U.S. is still recovering from the losses suffered during the pandemic, brands and retailers could benefit from manufacturing at least some of their clothes in America.
“American-made goods are overwhelmingly popular”, says Christie Grymes Thompson, chair of advertising, marketing, and consumer product safety for Kelley Drye & Warren, an international law firm, in an interview with Sourcing Journal.
“Consumer surveys consistently show over 90 percent of consumers [expressed] a favorable or somewhat favorable view of ‘Made in USA’ products,” Grymes Thompson says in a webinar regarding “Made in USA” claims. “A lot of people think it’s to help the economy, or to otherwise support their local community. Some people also think they would get better quality while recognizing they might pay a premium for that better quality or, at least, perceived better quality.”
Post-Covid, McKinsey & Company says it benefits retailers and manufacturers to move at least some production closer to home.
“Part of being resilient is building an agile network of suppliers and partners,” McKinsey states. “Certain major nondiscretionary retailers are diversifying their supply chains to mitigate dependencies on geographically concentrated suppliers. Retailers dependent on offshore production might explore alternative sources and locations, perhaps developing manufacturing capacity closer to core markets. Rethinking production footprints could help drive down risk while providing new value propositions for product that are sourced or made locally.”
Fashion brands that already manufacture their clothes in the United States, as well as those who are considering doing so, should consider that consumers value American-made apparel, and 90 percent say they would feel good about wearing clothes made with cotton that’s grown in the U.S., according to Monitor

research. Nearly 86 percent say U.S. cotton is something to be proud of, and 74 percent agree cotton grown in the U.S. is more sustainable than cotton grown in other countries. Furthermore, 62 percent of shoppers say they would pay extra for clothes made of cotton grown in the U.S.
When the pandemic spread in 2020, roughly half of the world’s disposable masks were made in China, but as COVID-19 became a global crisis, face masks became essential and countries started imposing restrictions on exports –unfortunately, this led to shortages of masks and raw materials. The pandemic educated the U.S. that we cannot just rely on China and once again, ‘Made in America’ and reshoring gained in popularity, especially for protective gear which grew about 60 percent.
Reshoring Means Reskilling
For U.S. manufacturing to become competitive, automation and robotics, are the key to offsetting higher U.S. labor costs. Manufacture workers need to learn how to use advanced technology, 3D design software, artificial intelligence, cloud computing, 3D printing and supply chain management – these are all instrumental in the continual efforts to reshore manufacturing.
Only automated manufacturing technologies will help US apparel sector successfully work out ‘local to local’ production more efficiently. (Photo Credit: Apparel Resource)
Substantiating on the same, Harry Moser says manufacturing costs in the U.S. are often 20 per cent higher than those in Europe and 40 per cent higher than in China and other low labor cost countries. “If we don’t invest in automation, we don’t increase our competitiveness,” he added. The fashion industry will have to think and talk technology, as only automated manufacturing technologies will help them successfully work out ‘local to local’ production more efficiently and successfully. “Some people are afraid of automation because they’ll lose their jobs,” Harry adds, but workers need to get over that frame of mind, “The U.S. will lose more jobs to Chinese automation if we don’t automate than we will to U.S. automation if we do. Since we are competing, you have to automate the best you can just to stay even.” Just like when Barthélemy Thimmonier’s sewing machine, created in the early 1800s, was destroyed by journeymen tailors who felt that the machine threatened their livelihood, we can’t allow luddites to keep us from moving our domestic manufacturing industry into the future.
Automated manufacturing technologies will surely and effectively help the U.S. apparel sector successfully work out ‘local to local’ production; while technology is integral to reshoring jobs back to the U.S.. And will provide higher paying jobs.
Reshoring Pioneers
As the reshoring movement gains in popularity, with many more to follow, one such fashion company that is leading the pack is American Knits in Swainsboro, GA. Companies like America Knits are testing the waters to see if the U.S. can regain some of the manufacturing output it relinquished in recent decades to China and other countries.
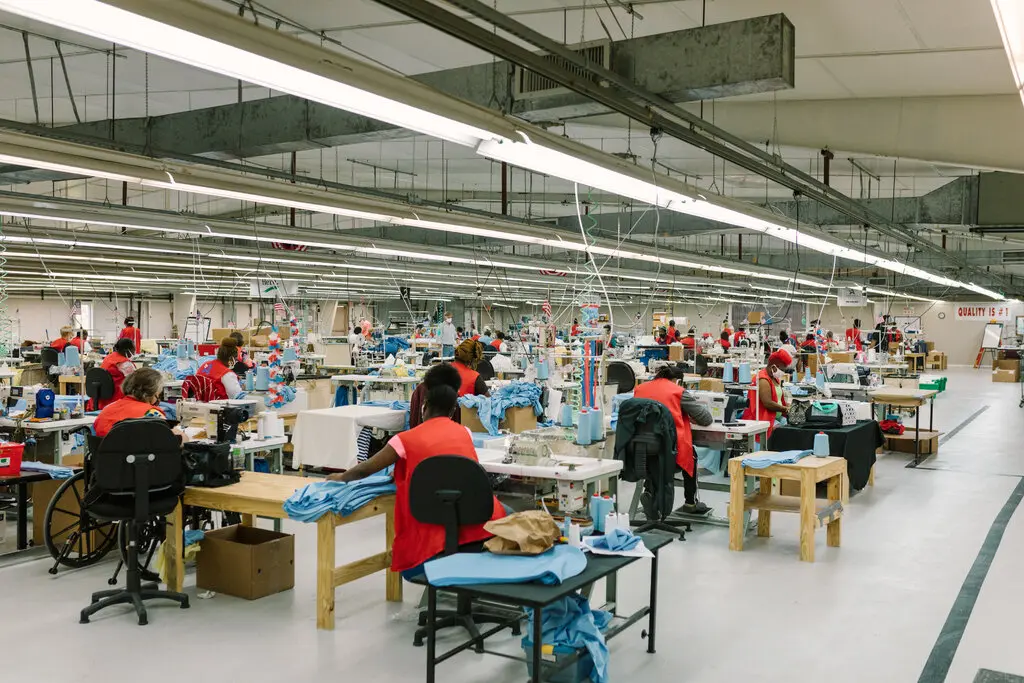
At America Knits in Swainsboro, Ga., workers earn up to twice as much per hour as they would in a service job. (Photo Credit: The New York Times)
American Knits was founded in 2019 by Steven Hawkins, with 65 workers producing premium T-shirts from locally grown cotton. He expects the company’s work force to increase to 100 in the coming months. If the area is to have an industrial renaissance, he is a visionary. “I’m the only one, the only crazy one,” Mr. Hawkins said to the New York Times. But as he sees it, bringing manufacturing back from overseas has found its moment. “America Knits shows it can be done and has been done,” he said.
Some corporate giant brands are eager to test that premise, if not for finished goods, then certainly for essential parts.
Since the beginning of the pandemic, efforts to relocate manufacturing have accelerated, said Claudio Knizek, global leader for advanced manufacturing and mobility at EY-Parthenon, a strategy consulting firm, in an interview with the New York Times. “It may have reached a tipping point,” he added.
Decades of dependence on overseas factories, especially in China, has been upended by delays and increasing freight rates — when shipping capacity can even be found.
Onshoring has never been more essential, not only because of the delays of much needed essentials due to the pandemic, but also for sustainability. Many companies have committed to sustainability, and therefore by manufacturing in the United States, companies will attempt to reduce pollution and fossil fuel consumption in transportation across oceans, which is a major selling point.
Julie Land is the owner of the Canadian company Winnipeg Stitch Factory, and its clothing brand, Pine Falls. The 12-year-old business is opening a plant in Port Gibson, Miss., in 2022. While fabrics will be cut in Winnipeg, Canada, they will then be shipped to Port Gibson to be sewn into garments like jackets and sweaters. The new factory will be heavily automated, which will keep her costs manageable, and the company will be able to compete with overseas workshops.
“Reshoring is not going to happen overnight, but it is happening, and it’s exciting,” Julie Land said to the New York Times. “If you place an order offshore, there is so much uncertainty with a longer lead time. All of that adds up.”
Another fashion company that is building facilities in the U.S. is Resonance, which is a collection of companies focused on transforming the fashion industry. The company opened its first sew production facility in New York City. The 300 square-foot facility is located in Pier 59 in Chelsea Piers, adjacent to the company’s headquarters. This is the first creation-to-customer-closet platform for sustainable fashion.
Resonance uses digital printing on organic and environmentally certified fabrics as part of a fully automated process to design, sell, and make garments in real time, on demand, sustainably anywhere in the world.
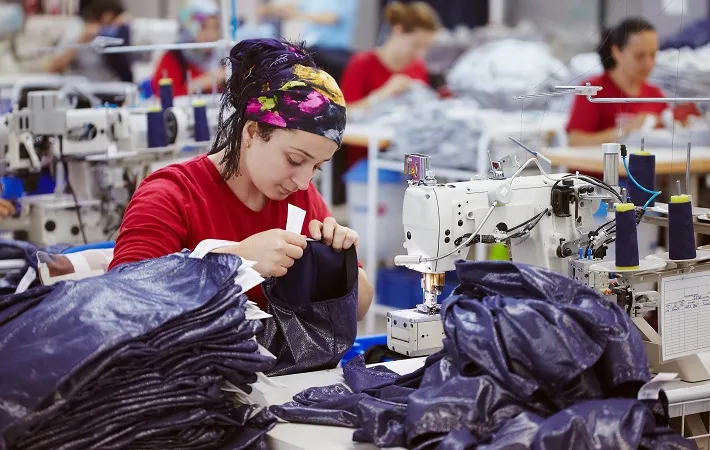
A Photo from Resonance’s New York City Factory. (Photo Credit: Shutterstock.)
“The new facility is comprised of 12 sewing stations with the ability to make hundreds of garments per week supported by Resonance’s proprietary technology. The team plans to hire additional team members to run the NYC facility as well as several others that are planned in the coming months,” according to the company’s statement.
Lawrence Lenihan, Resonance chairman and co-founder, said in a press release, “Resonance is deeply committed to bringing components of garment manufacturing back to NYC, a city whose thriving textile manufacturing industry was driven overseas in search of lower production costs,” the statement further said. “Resonance believes that this network can birth a new fashion value chain and new entrepreneurs can build job-creating manufacturing businesses in their communities powered by orders for clothing from brands on the Resonance platform. These next generation manufacturers will compete on cost and by being closer to the end customer, adding value to the last-mile process, and producing garments that create social and environmental value transparently.”
Resonance’s goal is to open hundreds of these sew production facilities around the country and internationally while also connecting existing ones, helping to reimagine the textile manufacturing experience for designers, consumers, and the planet.
Another onshore pioneer is New York Embroidery Studio, which is opening a new space in NYC’s Brooklyn Army Terminal. The new three-year lease is one of the largest in the Sunset Park location. The company has been manufacturing in the garment center for over 30 years and is known for collaborating with fashion luxury houses such as Caroline Herrera, Ralph Lauren, and Oscar de la Renta.
This luxury fashion company, known for their exquisite embellishments, pivoted at the height of the pandemic to create personal protective equipment like masks and hospital gowns. New York Embroidery Studio’s founder, Michelle Feinberg and her team made over 590,000 hospital gowns in just nine weeks and also kept hundreds of New Yorkers employed even as the city’s economy sharply declined.
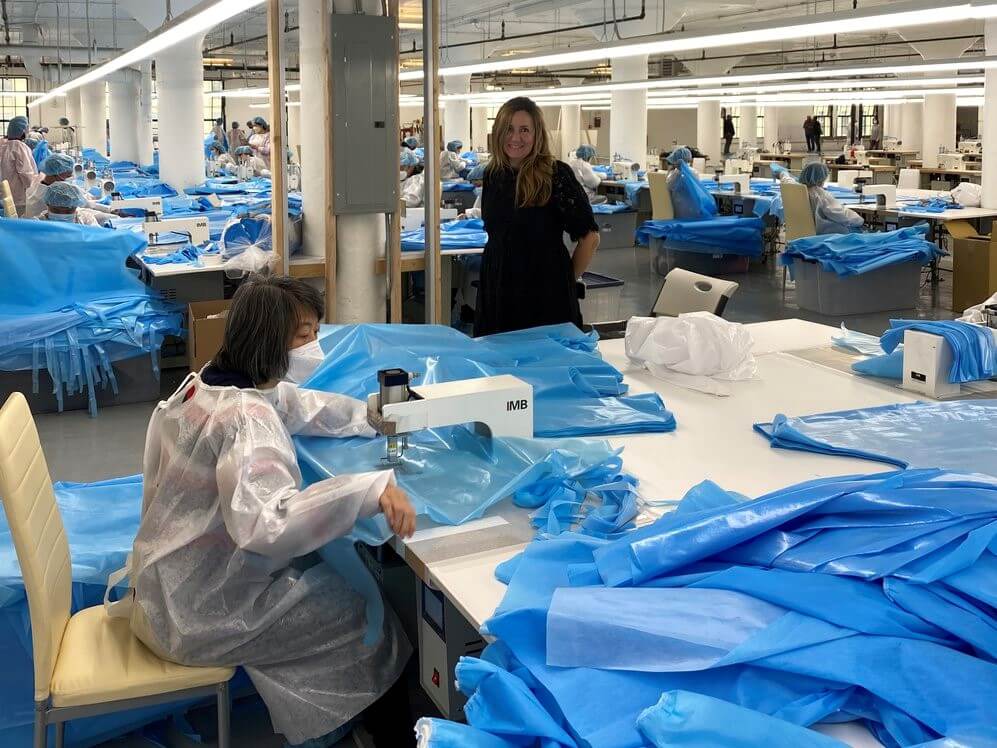
New York Embroidery Studio Founder Michelle Feinberg at the new Brooklyn Army Terminal space. (Photo Credit: NYES)
New York Embroidery Studio’s new 80,000-square-foot lease will bring more than 500 on-site jobs, generating an estimated $73 million in economic output for New York City. The studio will use automated machines and advanced manufacturing techniques to produce PPE full-time as part of an ongoing effort to restore the country’s national stockpile.
“The local production of PPE is essential to our health care workers and our city, so we are always prepared,” said New York City Economic Development Corporation President and CEO Andrew Kimball. “We must be forward-thinking as we address our city’s future pandemic preparedness.”
Russia’s War & Its Impact on Fashion Manufacturing
Since Putin’s war against Ukraine began in February 2022, the global fashion industry has come down heavy on Russia with brands refusing to ship merchandise and closing their retail stores there. Sanctions imposed on Russia are resulting in major supply chain issues for the global textile and apparel industry as the rising cost of essential materials such as crude oil and the rising cost of food is resulting in higher labor costs. According to Fibre2Fashion.com, “Several of the Asian economies are dependent heavily on coal and oil from Russia, and food supplies from Ukraine. UNCTAD [The United Nations Conference on Trade and Development] update on the Russian-Ukraine crisis shows that Turkey, China, Egypt, and India are the countries that are most dependent on food supplies from Russia and Ukraine. These are incidentally also major textile and apparel suppliers globally. Inflation in Turkey has skyrocketed to almost 54.44 per cent in February 2022, which is expected to significantly impact sourcing from the country. Consumer prices inflation in Bangladesh has also risen rapidly to 6.17 per cent, predominantly due to increase in food prices.”
The U.S. fashion industry (and Europe’s as well) is now having to take a long, hard look at what the repercussions are of their heavy reliance on foreign textiles and on shoe and garment manufacturing. Our once booming textile, shoe and garment manufacturing industries were reduced to rubble in the 80s and to bring them back will take time and lots of money. Watch this space as American ingenuity explores how to make it happen. It’ll take a village though: government money, fashion pioneers and entrepreneurs, patriotic consumers willing to pay more for Made in America products and an army of influencers to promote it.
Between the War in Ukraine and the global pandemic, these two events alone have educated Americans that reshoring is sure to become the biggest growth driver for its manufacturing industry – in particular the apparel and textile sector. As more and more companies explore onshore opportunities and align their marketing and selling strategies into the digital space, they just may be surprised at how profitable bringing manufacturing back home can be. Jobs, jobs, jobs.
So, tell us, how motivated are you on manufacturing your collection in the United States?
-------------------------------------
By: Antonia Sardone
Title: ONSHORE, RESHORE & OFFSHORE – BRINGING MANUFACTURING BACK HOME
Sourced From: www.universityoffashion.com/blog/bringing-manfacturing-back-home/
Published Date: Sun, 03 Apr 2022 23:55:36 +0000
Read More
Did you miss our previous article...
https://edmmusic.news/fashion-clothing/7-must-see-artists-for-bonnaroo-late-night-lineup-2021